StoneNode - Falling Rock Motion Tracking with EmbeddedLab Technology
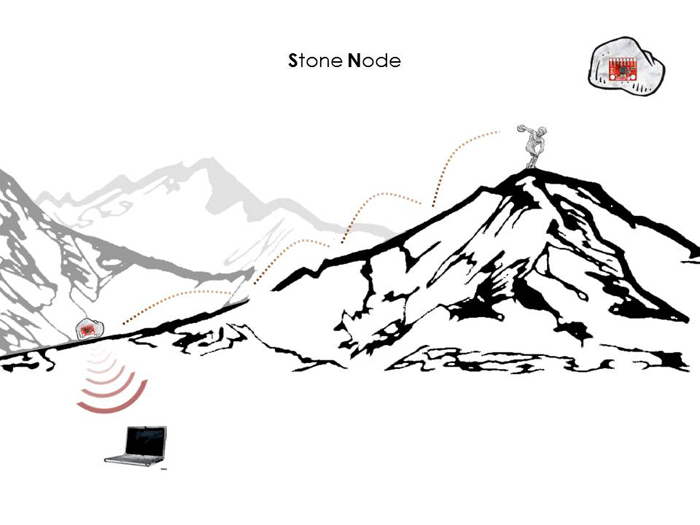
With the eyes of a electronic engineer, the aim of this project is to research, if there is a way using Arduino and it‘s embedded technology to track falling rock motion and rotation, as well as the decent and impact. The advantage would be, to have tiny, easy accessible, reusable and affordable electronics. This would also dramatically shrink the costs of every experiment in that field. On the other side, due to it‘s easy accessibility, it could be a possibility for students and researchers to build, program & maintain this kind of sensors devices by themselves.
The main task of the stone module is, to log sensor data properly during impact time! On the other side, with the eyes of a environmental engineer, there is no possibility until now, to measure and track small sized stones, that fall of the mountains regularly (>60kg). Such kind of empirical data would enhance software engineers to improve their simulator software with implications to the whole field.
This WSL financed project is a cooperation between the WSL Institute - SLF - EmbeddedLab ETHZ. The „Rolling Stones“ action will take place around Davos/Fluela area in the end of summer 2012!
09/08/2012 test on the slope
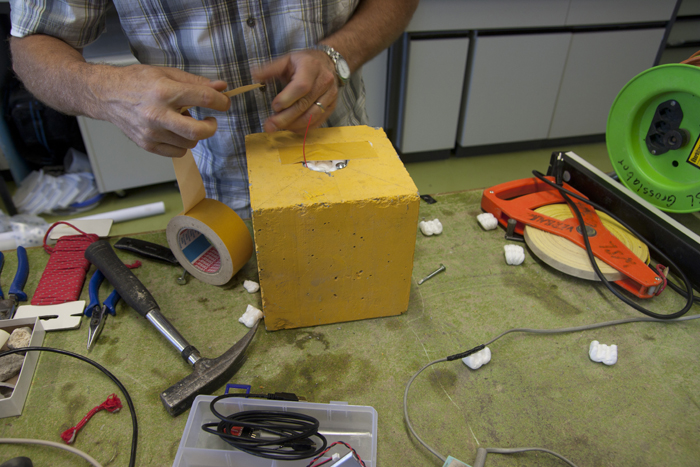
Experimental stone 20x20x20cm and 20kg with a round hole to place the sensor module inside.
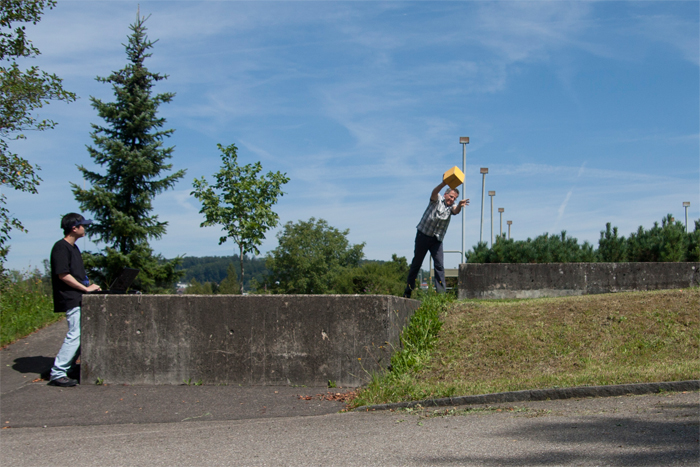
First field experiment at the WSL Institute (Federal Insitute for Wood,Snow and Landscape). We were pretty nervous because of the heavy impact that could destory our prototype (It is the only one we made)
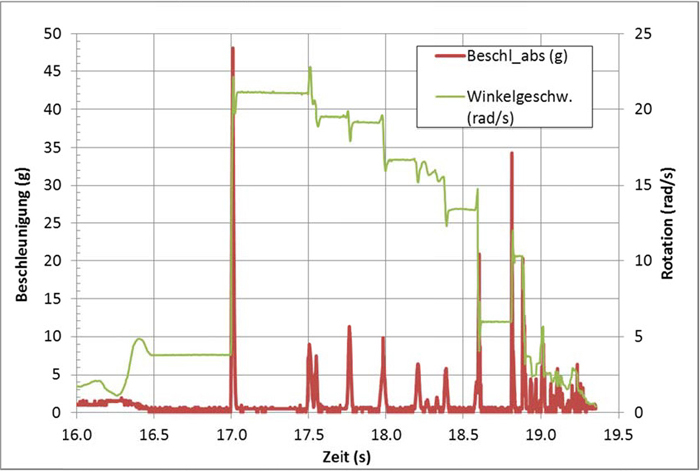
The evaluation of this sensor data looks very promissing for further experiments. The red line displays 3D acceleration and the green one is rotation in radian/sec.
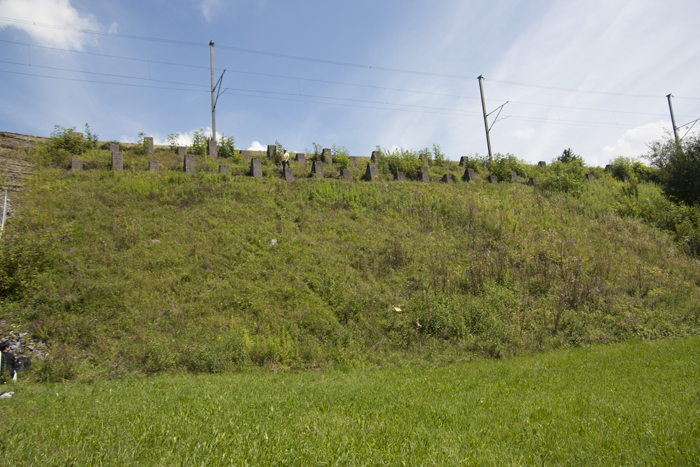
To get more results and natural conditions we went to a little slope near WSL. You can see the yellow stone tumbling down.
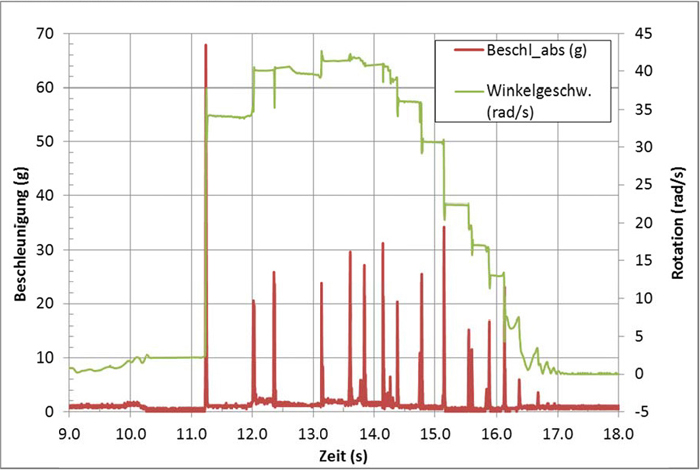
The results were pretty amazing, we could measure very precise data. Our enviromental WSL researcher colleagues were happy and sure to take the next step - direction Fluelapass 2300m. The only thing we have to work on in the future is the gyro sensor. We need a wider band, like up to 4000 deg/sec.
18/07/2012 test on the wheel
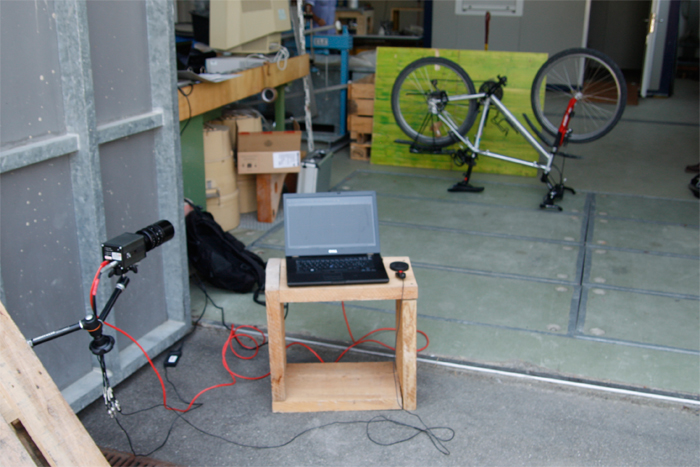
To veryfy sensor data and measurements in forehand, we placed the sensor module on a wheel and calculated the output by hand and then compared the results with the empirical sensor data.
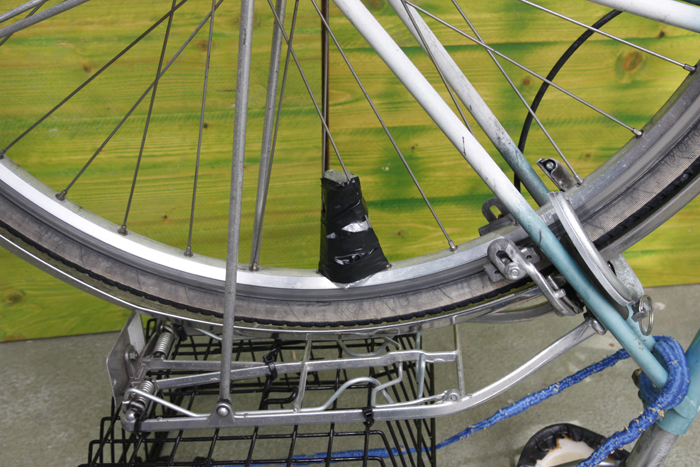
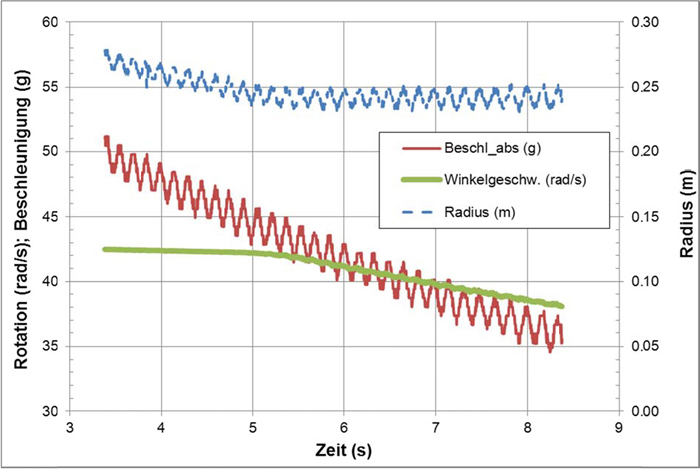
Now we knew, that the sensor data is precise, becuase the empirical outcome is pretty the same as the calculation/theory. The blue line displays the radius of the wheel, green displays rotation speed and red the absolute acceleration.
02/07/2012 shrinked and hand soldered prototype
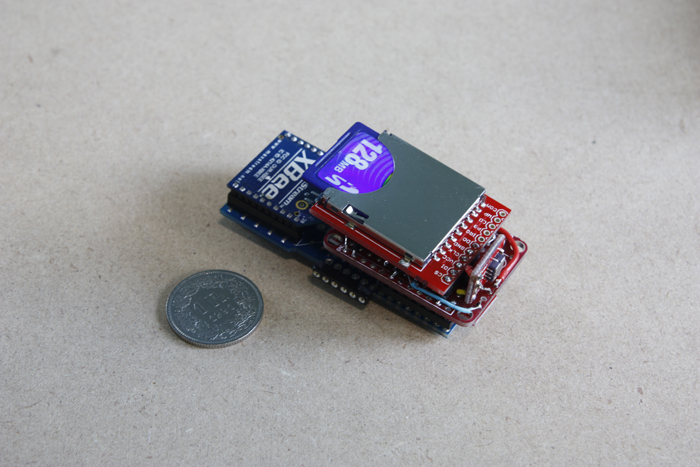
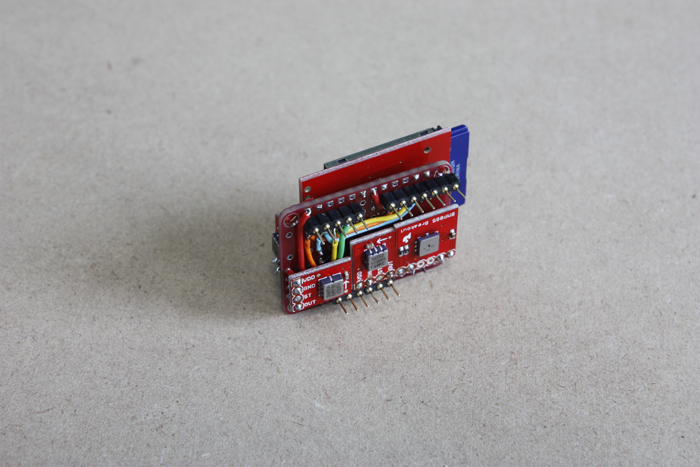
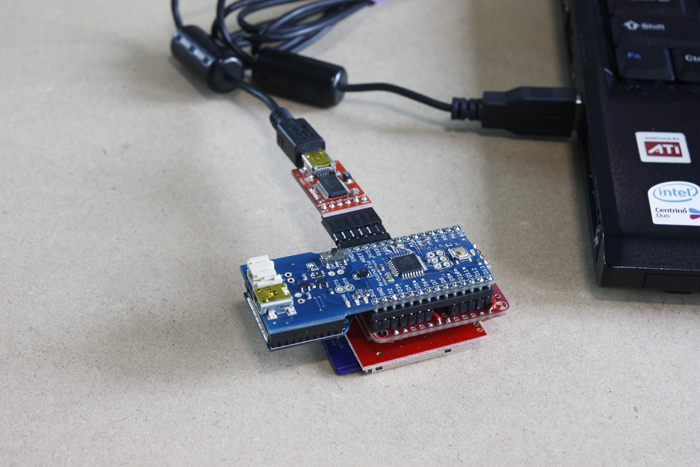
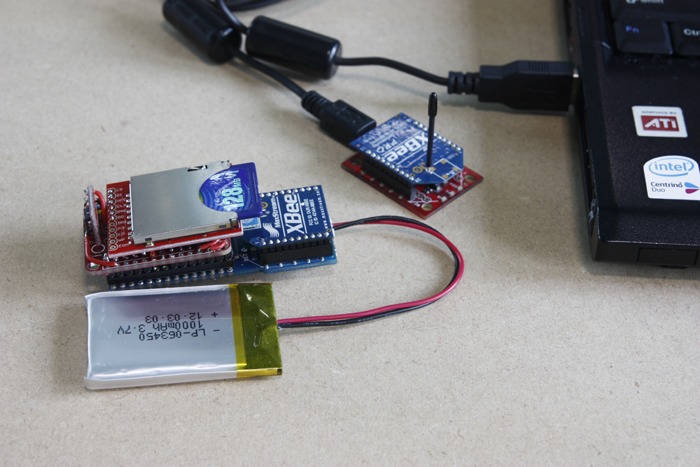
24/05/2012 3d model
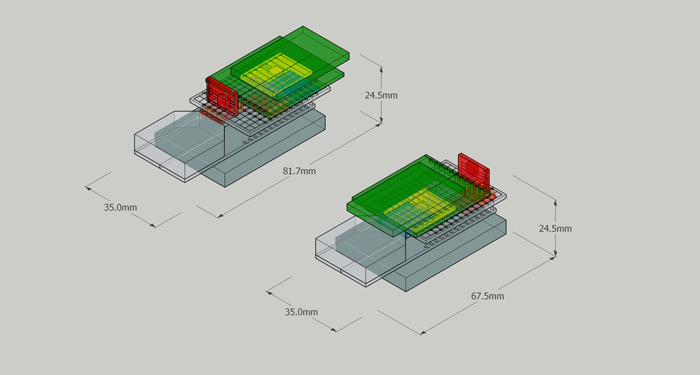
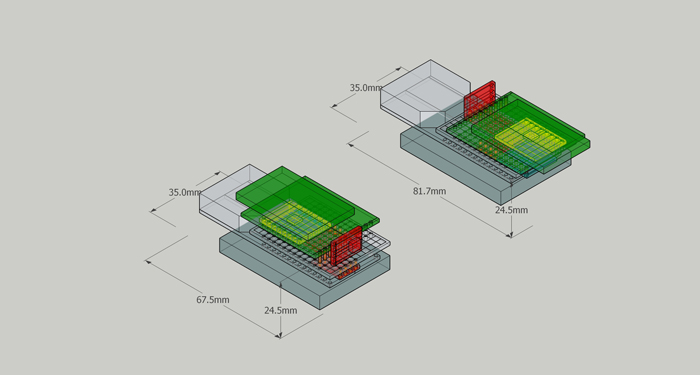
01/05/2012 second prototype on breadboard
After one week's testing, we found that the challenge is how to store the data with a relative high frequency. The eeprom we used in the first prototype needs 5ms to write each byte. If we sample 150 times per second and each sample contains 20 bytes, which means nearly 3k bytes per second, so the eeprom is not fast enough to record these amount of data.
After trying several different kinds of storages and protocols. We found that using SPI to read and write the SD card with raw data (which means without file system like FAT) is a really efficient way. Then we replace the eeprom with a SD card, the second generation came out. A xbee module is also attached to the soft serial port to transfer the data wirelessly to the computer, leaving the hard serial port for debugging.
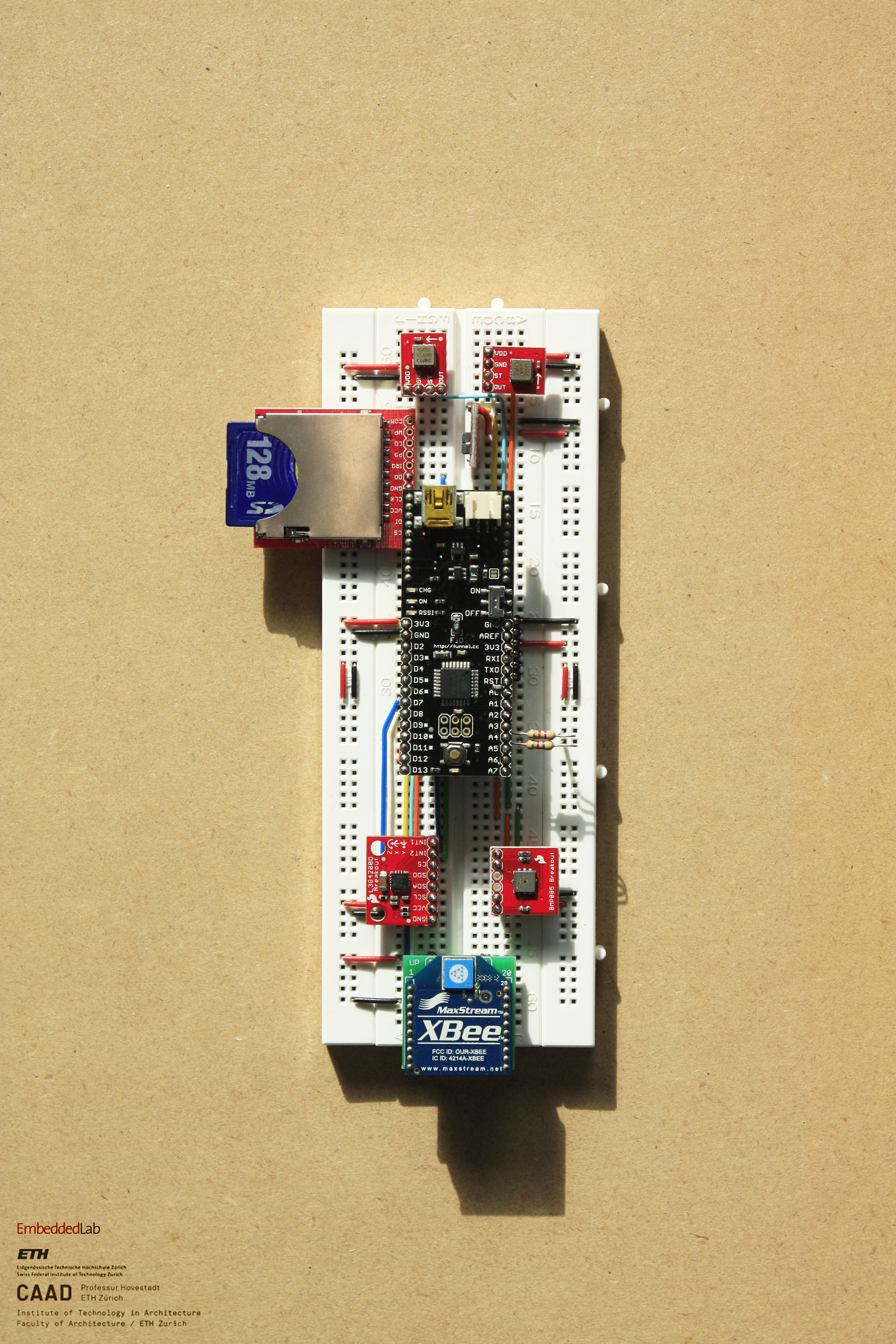
The second generation Prototype.
The raw data in byte stored in SD card are re-combined after uploading to the computer and saved as a CSV file. The CSV file can be easily import into the Excel and be processed for the further research.
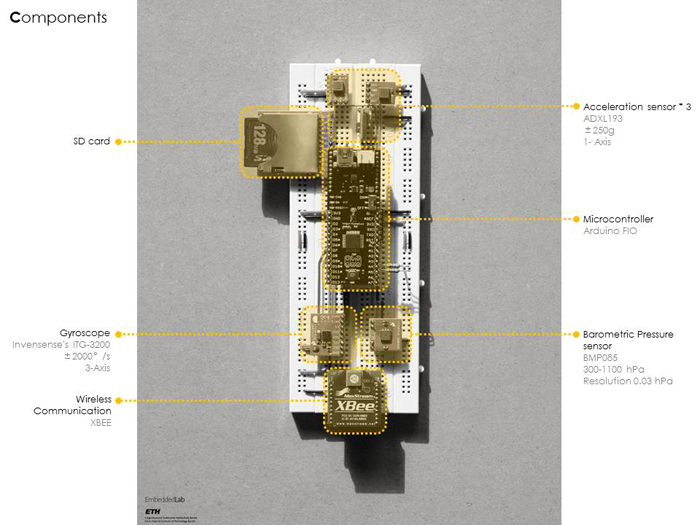

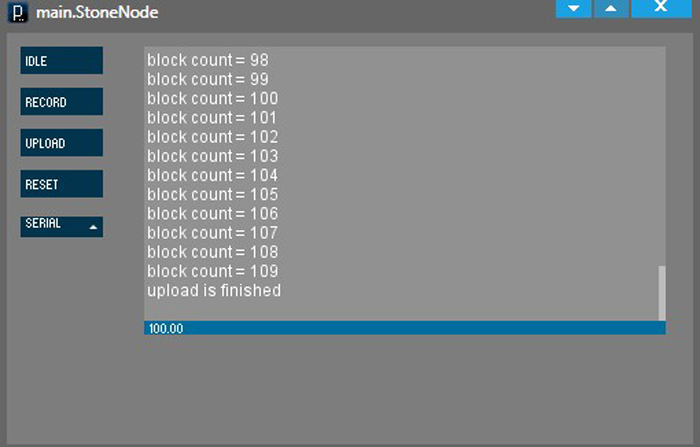
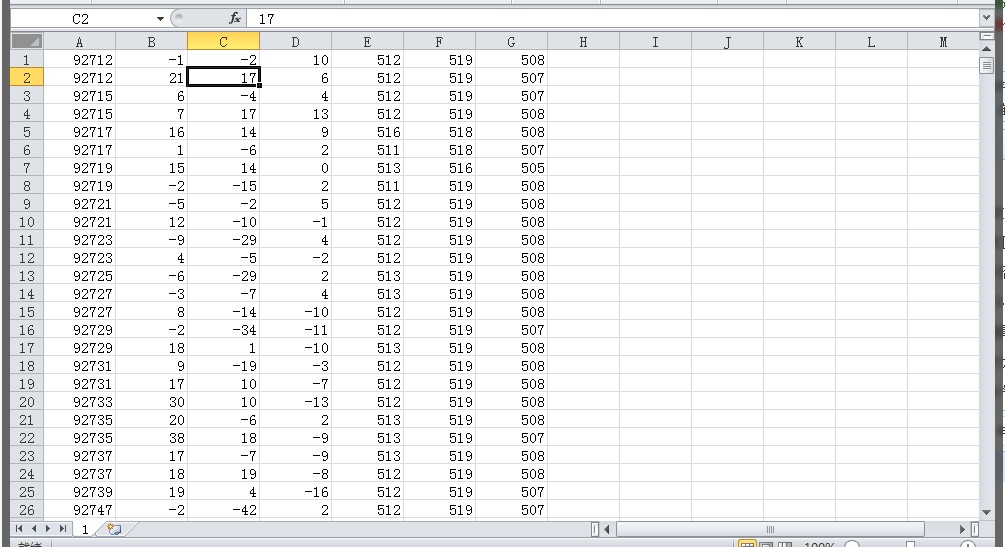
The CSV file.
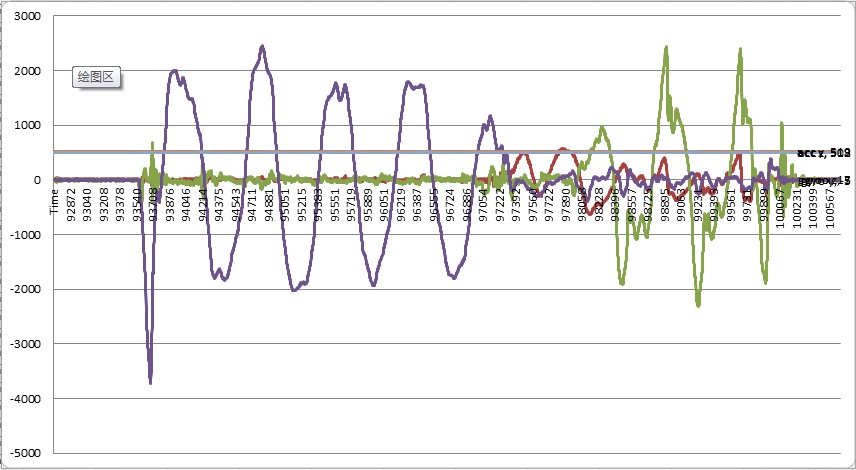
The chart in Excel.
21/04/2012 first prototype on breadboard
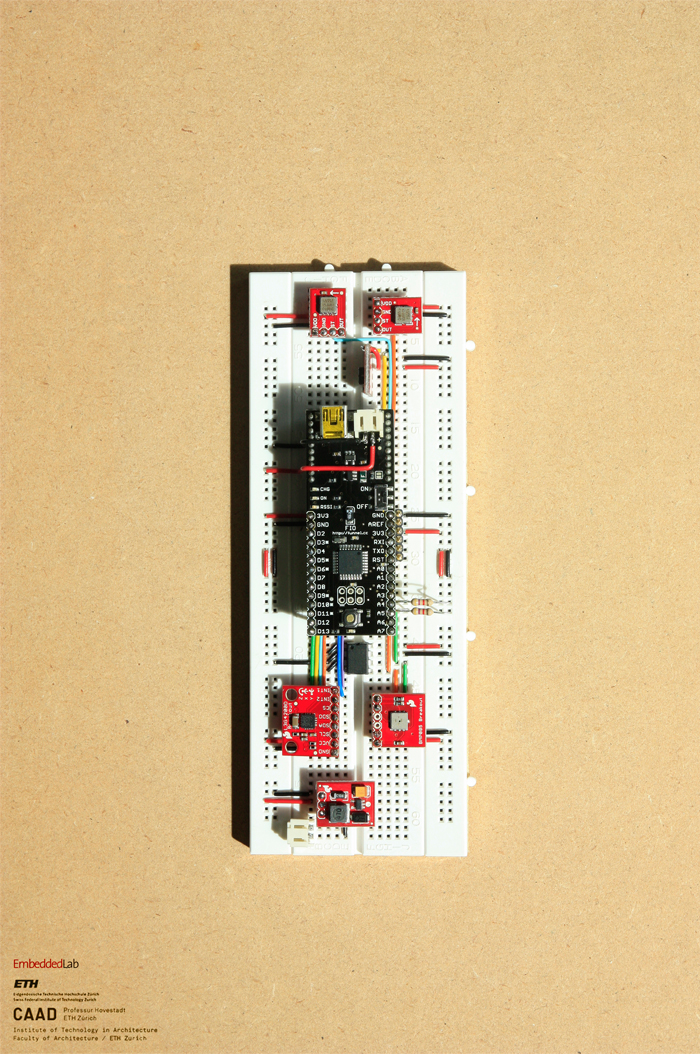
The first Prototype.
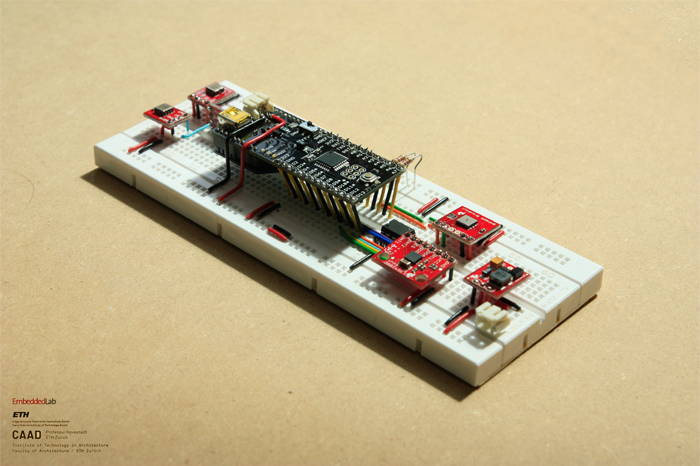
The first Prototype.